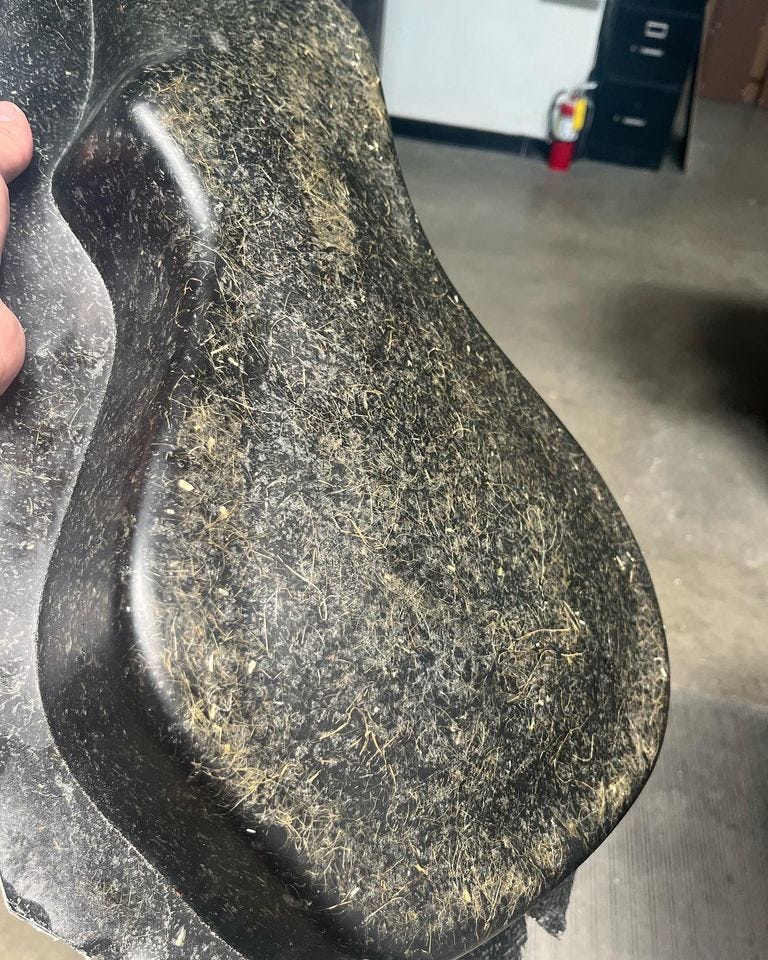
About 10 years ago, I identified the fingerboard of the GuitarViol as the essential keystone to the instrument; one which conventional approaches were unsatisfying. Unlike relatively flat guitar fingerboards, installing fret-wire on a geometrically complex playing surface was a bloody fight against physics! A major bottleneck for the first decade +). Guitars are easy, GuitarViols are difficult to get “just right”. A major bottleneck and probably one of many reasons the original Arpeggione failed for 200 years! Between 2010-2013/14 they were typically roughed out on a CNC (computer guided router) and jewelry wire was embedded. Even with CNC, the man hours were insane to get it to a finished product! (I could do better by hand, but demand always outpaced me). There were other issues. The steel wire ate fragile (expensive) cello strings for lunch! Also, organics (wood) had hidden variables causing hot spots or dead spots (i.e. one note louder than another). It was a crap shoot every time with a week (actually two) of labor involved to find out! (Guitars are way easier). The question had to be asked: “regardless of tradition, bias, snob foolery, or material, what would the ultimate playing surface be like?”. The first ViolGlide fingerboards were born and there began my foray into composites!
There were a few good (ViolGlide) boards (at first) but they still took a significant amount of corrective work! (2014-2015. Here I was trying to up the quality and it was still a bottle-neck!). The early silicone molds were problematic in heating up and distorting the part; causing massive bandwidth sucking re-work. Since I was also considering carbon fiber as a construction material down the road, I reached out to Alistair Hay of Emerald Guitars (Awesome!!) in Ireland. [Concurrent with a zoning foisted 2015 move from Sylmar CA. to Fillmore.] I shipped him a master plug (mold positive) and months later, we met at NAMM and he handed me my first proper composite mold minus $1800 bucks. There were some instructions. In the end, that mold did not work out though it was an important learning a step in steep learning curve! [By the time I received that first mold from Alistair in January 2016, I had just committed to the 10xBETACF (Carbon fiber GuitarViol project that would be the most epic climb ever!) Once I figured out that particular fingerboard mold was not going to work as hoped, I went and made another myself based on what I did learn from the one Alistair made. (Part of the composites hazing process as I have found out! Thanks for the heads up on the steep learning curve Mr Hay! The second mouse gets the cheese!) I had to completely re-engineer the materials and processes to suit precisely what I envisioned these fingerboards to be. (Took a minute). The best of materials and close to zero friction Teflon like performance lubricity. There were some initial fails and it took a few months of suspended shipping to get it right! (Ouch). Lots of studying relevant composites papers from India! Late summer of 2016, a few fails, refinements. and dogged tenacity = success! All fingerboards since have been made that way since! But this was just the beginning! The rest of the 10x would be designed around the ViolGlide fingerboard!
The remainder of the 10x tooling had to be made though! My confidence in making molds was significantly better at this point. I really thought that I would have it launched in 2 years +/- but it was more complicated than that! You see, I had to ship my other extant models (30 or so a year) WHILE making the other molds on odd evenings and weekends whenever Mrs. would not kidnap me from the shop! (The public really does not understand the ice beneath the surface of this 10x iceberg!). [*Attempting Yamaha level engineering without Yamaha level and capital is not recommended for the gatherers of low hanging fruit and quick ROI]. If the mold making was not epic enough, other complications came into play! We moved into the Fillmore shop in May 2015 due to a LA zoning conflict eventually to be met with more hostile bureaucracy in the City of Fillmore at the beginning of 2017; right after I built walls to contain the climate for (wooden models) no less! UGH! The owner of the building was at war over occupancy/zoning issues with the city and there was a dark cloud of uncertainty hanging over my newly minted shop over the next two years! (I was really not up for the stress of moving again so damn soon!) Freshly recovering from a previous zoning hassle/move out of Sylmar! Plus, the friends in the building were awesome people to be around! Good times! Things got ugly in August of 2019 when the building was red tagged by a corrupt city hall; a genuine “you can’t make this up” story! (A case study with a script for another day). I was so pissed to have my operation disrupted (again!) that I hit Loopnet and found an “up to code” space in friendlier Valencia. 2.5x overhead $$, in October, moved in November 1 2019, right before the pandemic shook things up again.
(“How’s my 10x coming along?” Grrrrrrrrr….).
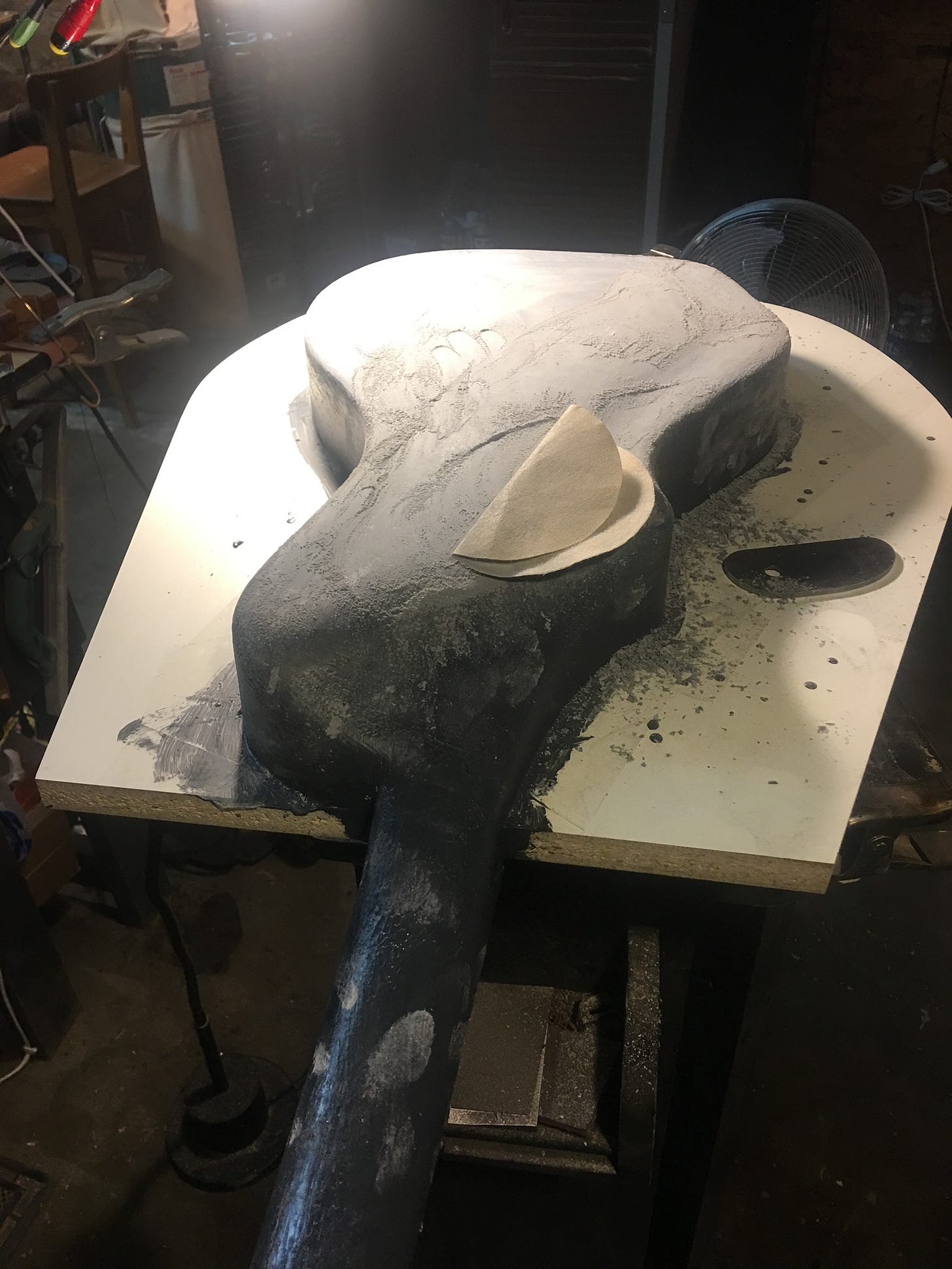
What did this have to do with composites and the 10x? Well, the project clearly had more sand thrown at it than I ever imagined! (The story is the process?) If the engineering was not daunting enough, the circumstances I navigated were not anticipated (in the plan) to say the least! Sure, all the molds were made in that turbulent (otherwise happy) Fillmore era, but, the engineering and trials were still to come! Meanwhile, California’s new AB5 (anti-freelance law effective January 2020, 1099’s became Kryptonite in California) changed the dynamic of offsite work I could delegate to trusted freelance hands on an ad hoc basis. If that was not enough to process at once, there was the added confusion and chaos a pandemic brings! By mid 2021, my son Andrew left for greener pastures (proud!) and I was 100% alone in a nicer albeit “compliant” “up to code” shop, with higher overhead, in bourgeois hating California, with the flaccid economy that followed. (Seriously? We all have to suffer this stupidity?) OK, That meant 10X OR BUST! On one hand, this period presented a perfect shop setting to tie up loose engineering stuff and get the project launched! On the other hand, the increasingly wonky times and new economic constraints also slowed it down. Distracting! Talk about TRIAL BY FIRE!
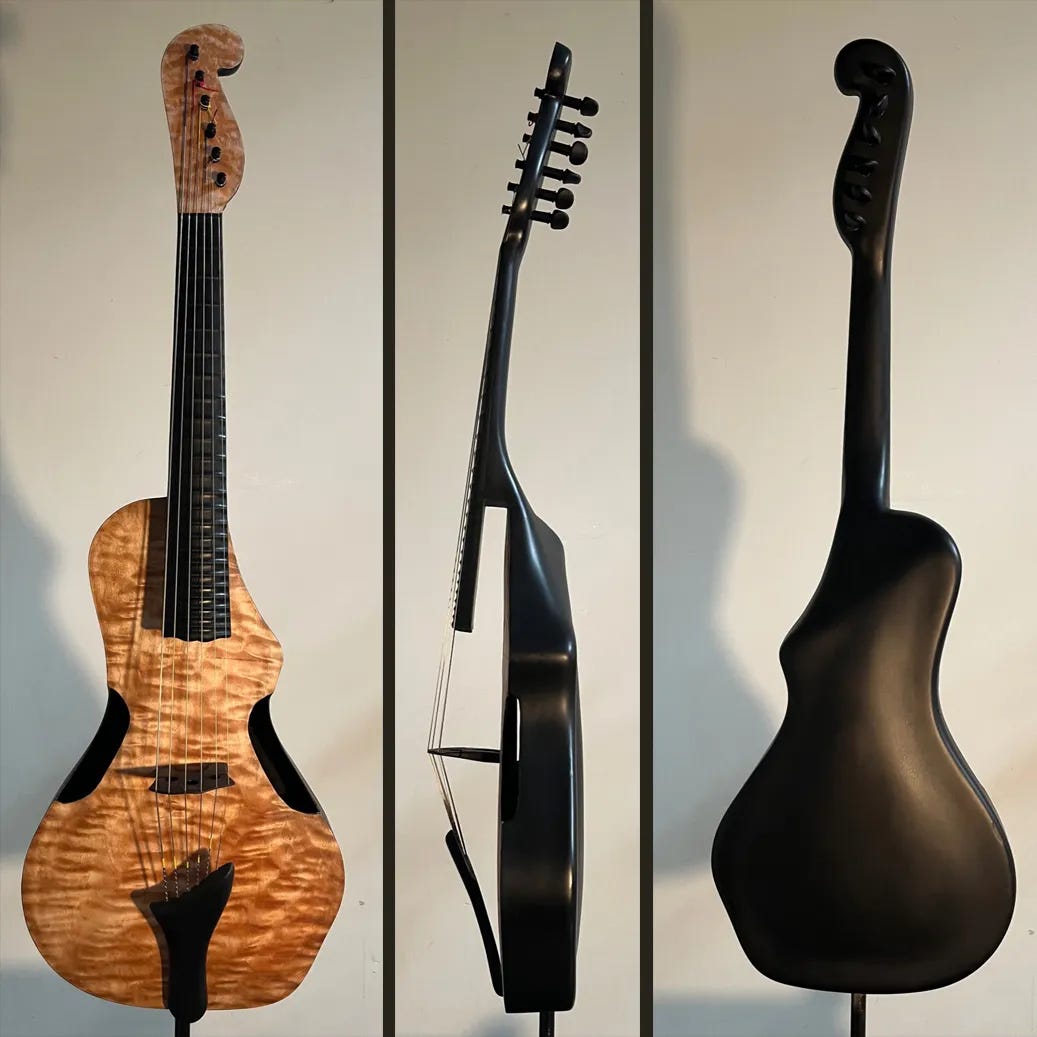
The initial 10X hulls were, to original plan, and made of vacuum infused carbon fiber. The first draft was encouraging in terms of feel and sound! Onto something! However, I was confronted with months and months of working out some structural things as well as finding out just how BRUTAL carbon fiber is to finish!! [bottleneck multiplier alert]. The world demanded my stuff RIGHT NOW/YESTERDAY, but complicated reality and the actual time required did not match up! This was pivot or die and the months went too damn fast!! UGH! Simultaneously, I was building away (burning the ships) the last of my wooden model stock and keeping the lights on while other business park neighbors were shuttering! (Sad!) Talk about a juggle! Stress? You bet! Little by little, solutions to the carbon fiber coating issues lead to flax veil (from Germany) for coating base (which were a positive enhancement to the sound as well!). However, the finish work was still epic (though much more approachable than raw CF! Progress!) Eventually, I had to look for domestic alternatives to the Flax veil I was using as importing it from Germany was ridiculously expensive and potentially disruptive (the times). I did, however get some encouraging results with this (great product) as a veil over Flax cloth (instead of Carbon Fiber). I am onto something! Process of exploration!
Besides Flax, I was also incorporating hemp cloth on the maple/balsa/hemp vacuum infusion tops. The sound was ridiculously powerful/dynamic! It smokes the Spruce tops of before! (Yes, attendees at last years meet-ups noticed!) For the hulls (main body neck part), I thought perhaps there may be a non-woven hemp that would replace the Norafin as a veil layer? It turned out to be quite the combo with flax cloth (in place of carbon fiber). This is great because the look is compelling and I am beginning to understand subtle colorful ways the hemp looks with a blackened flax cloth background (for instance). You see, both are fast high yield crop domestically and, when given composite treatment not unlike carbon fiber/kevlar/glass cloth approaches, more possibilities and outcomes happen! When given resin vacuum infusion treatment, these fibrous organics become a Super wood! Easy maintenance and no sweating wildly fluctuating relative humidity. No cracking. Just joyous performance, feel, and sound! Engineered from an instrument maker’s heart and application of known physics and classic design aspects.
Composites and instruments go back a lot longer than many people realize! Lutes were a similar combination of veneer and linen cloth soaked in hide glue. I remember an episode of Museum Secrets where they replicated medieval armor plates made of flax and hide glue. They were lighter than metal (which was rare anyway) and indeed this combo resisted arrows piercing! (yes, they tested it!). Point being is that fine instruments can be made from organic composites in an additive approach with patterned hand crafted molds! Subtractive approaches involve removing material (carving and lots of waste on the floor). Additive approaches involve deliberate application of materials to a precise pattern (less waste on the floor) with an artistic caveat. Much like paper mache’ with serious materials. Composites are not limited to carbon/kevlar/glass. They can include organic substrates as well. What I call Organic composites, others call Bio-composites. Either way, there are options that would please green tech folks. I am not green washing but do enjoy working with less nasty (safe) materials and the engineering challenge to bring them to life just as I have with hundreds of other hand made wooden shellac polished instruments over the last 20 years! The same love and more! Keeping the fun alive and adapting! Next level even! Master of Green Ghetto tech!
There is wisdom in tradition; Time tested principals to rely on. Remember, tradition came from somebody’s successful discovery that was worth repeating and stood the test of time. Discovery comes from the willingness to blaze new trails and take the thorns. Without discovery (i.e. someone actually trying to go next level), the state of the art stagnates and atrophies. If Antonio Stradivari were brought to the present in a time machine, one may speculate that he would marvel at how the work of his lifetime remained virtually unchanged! (Actually, his fame happened long after he was alive). He may be amused with the modern tools and machines. He may say something like “I had a lifetime and you had centuries! What have you done with your time?” He may also find it amusing that his works command a kings ransom at an auction? Who knows?
What is possible is exciting; Like the instrument itself! However, it turned out that modeling to the past has it’s limitations; the very ones that made this (Arpeggione aka GuitarViol) instrument fail for two centuries. If one insists on wood and hide glue construction with sheep gut strings/tie frets, then there is always the Viola Da Gamba. [Turns out, some GV clients have also explored VDG and early music on the side! Full circle!] The difference with the GuitarViol is that it has contemporary (modern) aspects that lend to blending Rock guitar vibrato with Classical (for instance). Or that Hendrixian feedback (complex multi-phonic harmonics) without a Marshall stack expression of the bow! The other is having modern bowed strings (higher tension than sheep gut) for rich orchestral and solo applications. Highly responsive! This has been a boon and major feature for Movie Soundtrack composers of the last 20 years! So, you see, that instrument that failed for 200 years (and most people do not understand) took some doing; in fact a lifetime to be viable. Some luthiers have attempted this but have abandoned it after unsatisfying results. Unlike guitar or violin making, this guitar formatted Viola has it’s own set of problems that required solutions outside of the generally accepted approaches. (The generally accepted approaches do not work well). It takes an ill advised life long devotion to a craft few understand. I offer these Guitar Formatted Violas for those who can appreciate it. They are not toys from a factory. No low hanging fruit here!
…………………………………………………………………………………………………………………………………………………………
In the mean time: Preoccupied getting through all but impossible logistics. The Documentary is going very well, more on that soon in a different essay. I’ll also be writing about other peripheral stuff on days my body gives out from the wear and summer heat! More announcements to come as I have to assess re-set the operations increasingly impossible ETAs and an eye on abating backlog whilst filling the gap with pop-up rack pieces. Moving forward with all my might! Have a great week!
Faithfully,
Jonathan