The ONE model of GuitarViol…
A turbulent Journey through the circles of purgatory to musical paradise
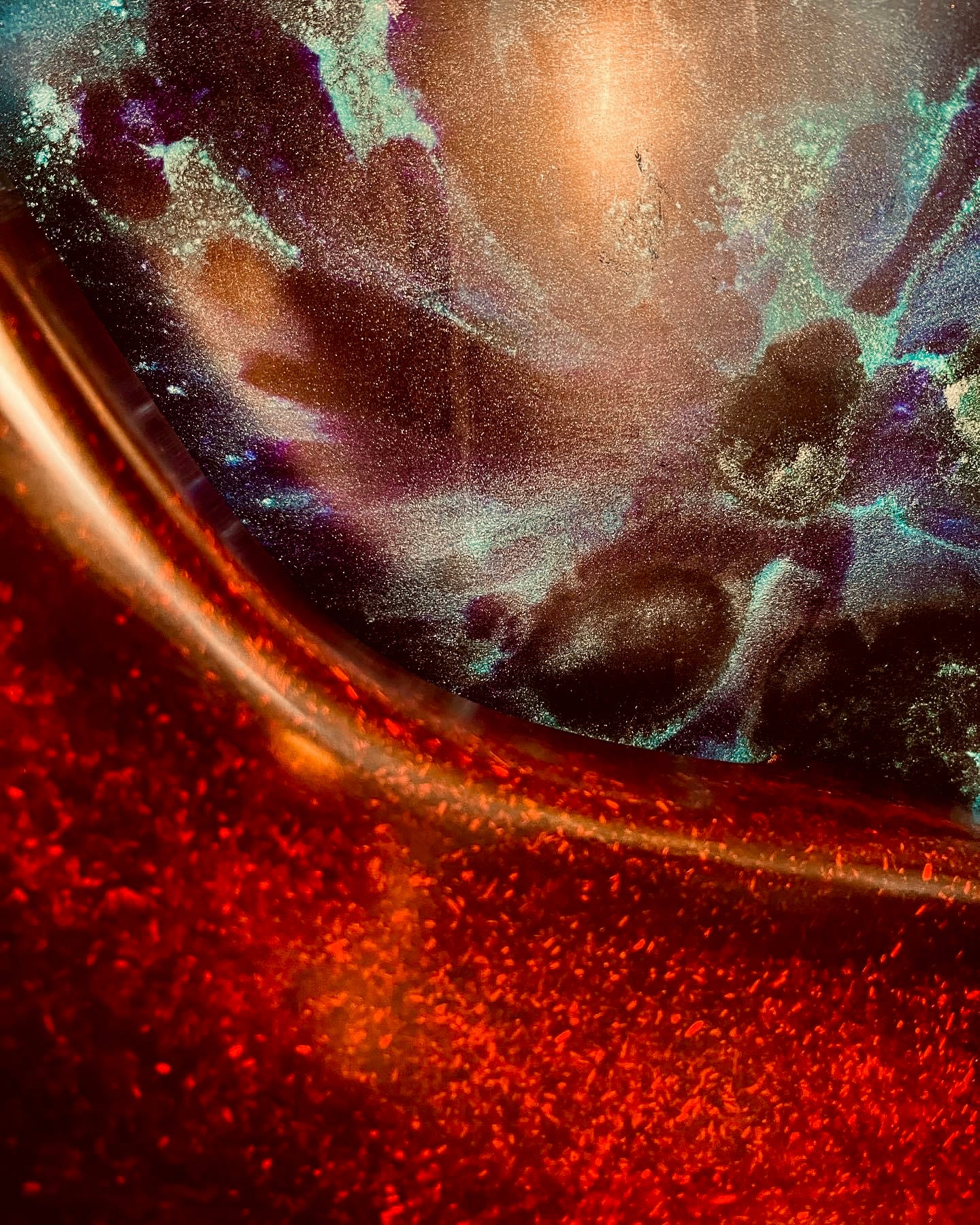
Many long time readers know some gist of the story. I started chasing the Arpeggione in the late 1980s. Obsession became reality by the early 90s. By the Y2K’s a shorter scale ergonomically driven version was prototyped and rebranded as the TogaMan GuitarViol. Unexpected demand (for the new one) had me scrambling to put these in some sort of production. With a growing queue, I had to stick to the template. Deers in the headlights will never understand! “I want mine like this” “I want mine like that!” These were very strange things for me to hear because I did not intend this instrument for other people (though I did make templates just in case). It was not to be the average of what people wanted! It Stood alone as it’s own “thing”. Unapologetically so. With demand stacking up I had to follow a consistent pattern to get it done. Custom unicorns and goblin inlays be damned! All of these customers with IMDb profiles were anxious! Throughout the years I’ve been mistaken as a custom builder. In truth a limited production builder. (how did I become a builder at all? That was not the plan!) However, I had no choice! The first ones being built by my hands were the fruit of my frustration of communicating my plans to an interpreter (other luthier) who would generally foist or hijack the project to do it their way! Been there too many times! Delegation leads to repeat frustration! I was having NONE of that! So, enter the old rusty bastard file, blistered hands, and a dream! Straight from the source; Interpreters be damned!
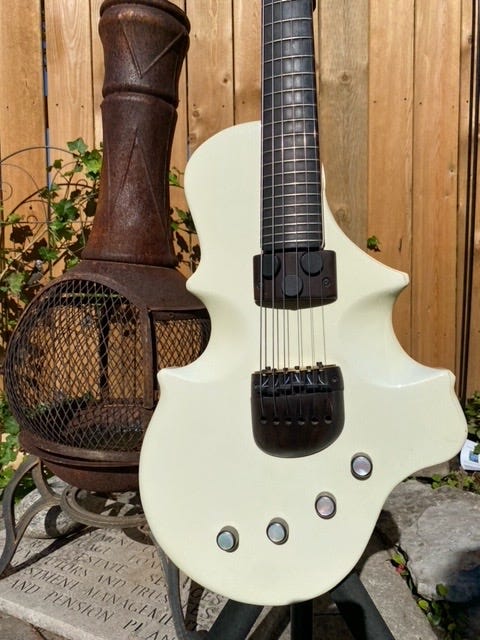
Between the years of 2002 and 2009, I built a Particular solid body electric model that gained some popularity. It went over huge in the movie 300 (A very big deal at the time!) it was a true hybrid model at the 50 yard line. It was neither 100% optimal for bowing nor 100% optimal for plucking (guitar playing). It was initially meant for my standalone looping performances; A continuation of what I was going for in the 1990s. Truth be told it was a logistical nightmare to build! (too many vendors and too many parts! = too many bottlenecks!) It required custom machined bridge blocks (a bane and a bottleneck; at the time something outsourced that would hold deliveries hostage!)
Somewhere in 2009 I had patterned an “in between” model called the ElectroCoustic. At the time I thought it would create a pressure relief valve for the bottlenecked solid body models. It would offer a more “acoustic” response than a direct Piezo electric response. It was meant to be plugged in but surprisingly it had some acoustic sound that could be miked. Perhaps I was trying to create modular builds that could be made offsite at a later date. Initially I wanted all of it to be done “in house!” However a local friend with a CNC machine had enthusiasm that ran over me! So long as the patterns were cut to precision, what could possibly go wrong? (Not so fast, not so smooth!) Let’s just say about 100 of those (ElectroCoustic) models were made over the years 2009 through 2019. Although many of those particular ones are well recorded and still in service, by no means were they my favorite model! In a sense I was solving one problem by creating another! Ugh!
In a parallel universe, there was growing interest in the acoustic models! The first acoustic was prototyped somewhere in 2006. The concept was a bolted in neck heel much like Taylor Guitars. (This was not working out well) Eventually I would do traditional violin style attachments. (again this modular assembly thing was not working out). That particular acoustic (made of Purple Heart back and sides with a curious ugly flat top) was loaned to my friend Barry at Guitar Player Magazine. When DHL brought it back, The box was run over and the top was smashed! To their credit, DHL honored the damage claim and I shrugged it off as an opportunity to test out a newer Side port design that has since been repeated in the hundreds! (2024: Ibanez recently copied my stereo port design on their ukulele - really guys?) The first top was made of pine because I wanted to test the concept rather than mess up A good block of high-grade AAAA spruce. I did not want to sell this particular one because I was embarrassed by the “wrong” wood choice that sounds so amazing, KEVIN KINER bullied me out of it with an offer I could not refuse! (yes that one was called “old faithful” and has seen a lot of movie score action! still in service today!)
However people were making buying decisions (acoustic vs electric) based on cost and not what they really wanted. The electrics were at one price point and the acoustics were significantly higher. So I decided to try an experiment! I committed to building seven acoustics at the same price point of the electrics! It was called Experiment 7. The concept was to load the queue and build through them. If the price point wound up not working on my end, I would discontinue after that seven commitment! Spoiler alert: it worked! (but I would spend the next several years ahead improving processes to eventually become what is today: the 10x).
This created another problem! I had three basic model types: solid body electrics, semi acoustics, and acoustics. All of which could have pick ups with varying degrees of sound. One problem was it caused a lot of confusion for buyers! And during those years between 2012 in 2015, there was some upheavals with regard to venue (where we lived and worked). One place we had between 2008 and 2012 came to an end when the landlords toxic loan did not age well. From 2012 until 2014, we were happily moved up the street until some hater threw my garage operation under the bus with the city of Los Angeles building inspector. That led to the Fillmore era 2015-2019 (another story). Those particular times (before Fillmore) I was a little too preoccupied with venue drama to go into massive engineering mode and I continued producing the three model types. Once settled in Fillmore, I came up with the concept of the 10x universal design made of composites. Initially carbon fiber.
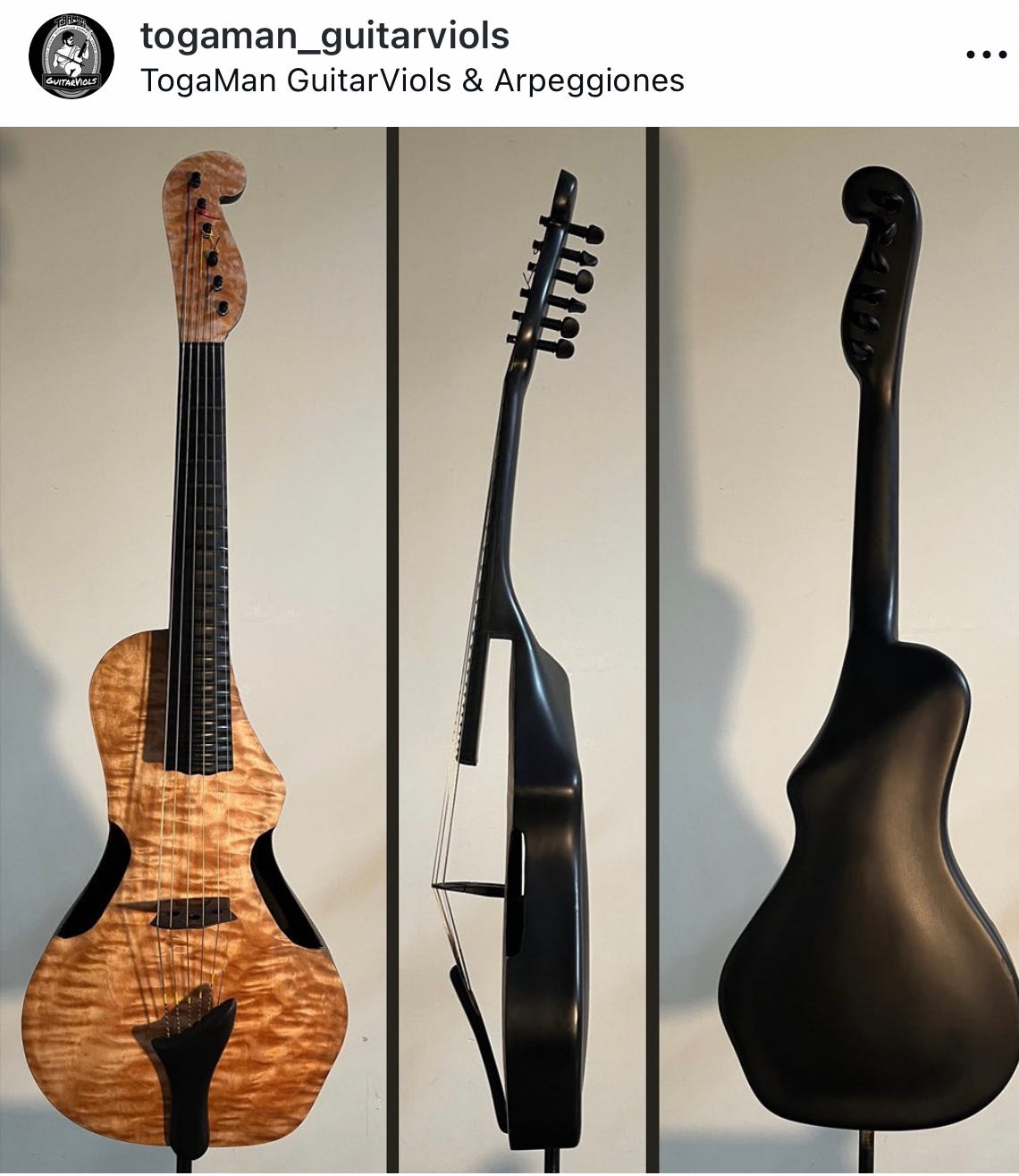
The Fillmore shop was a hard landing! It would take another year and a half to get the shop space suitable. The first winter destroyed a couple jobs and we had to make some humidity barrier walls between Christmas 2016 and New Year’s 2017. That worked! But I was still managing three different model type fleets! Fortunately I had some peers in the building that came in handy. On the other hand, I had to solve this problem of too many options! Over time, I would pare down the menu. The goal was to make the 10x design the ONE model! But that would prove to be a very slow, painful, and turbulent Crossfade!! Not just for the reason of massive engineering; there were contrary external events happening! One was that we had trouble with the city of Fillmore over occupancy issues between the city and the owner. By itself that was a nightmare! (bureaucracy bites me once again! So soon after LA zoning problem? ooooof…) This culminated in a red tag shake down, being locked out of our shops in the summer of 2019, and ultimately a move by that November! This coincided with California’s freelance busting law AB5 that impacted not only some of my logistics, but also that of musicians in California (my clients). Then, if that was not enough, there was a pandemic with all of the confusion, muzzle fest, lockdowns, supply chains, rapidly changing customer priorities and behaviors. All of this in the middle of the 10x transition! Dammit! Just dammit! Dammit dammit dammit Grrrrrrr….
So, The new Valencia shop, in all of its awesomeness and double expense $$ was the UNPLANNED venue for phasing out the old wooden models (burn the ships!) and phasing in the 10x. That would’ve been hard enough before. Doing that smack dab in the middle of pandemic chaos with diminishing cash flow and manpower was another thing! NOT THE PLAN! Up until the summer of 2021, my son was working there and eventually his expiration date (burn out). From there I was left alone to not only keep some semblance of wooden model production phase out, but also to get the molds that I had made in Fillmore between 2017 and 2019 up and running! That took many months of trials, Errors, and eventual victories! (try doing that with all the “are we there yet?” Passengers pecking at me in the middle of a toxic trickle hemorrhage of resources consistent with the times! I dare you to understand that!) 10x or bust!! (ever tried juggling cats and chainsaws?)
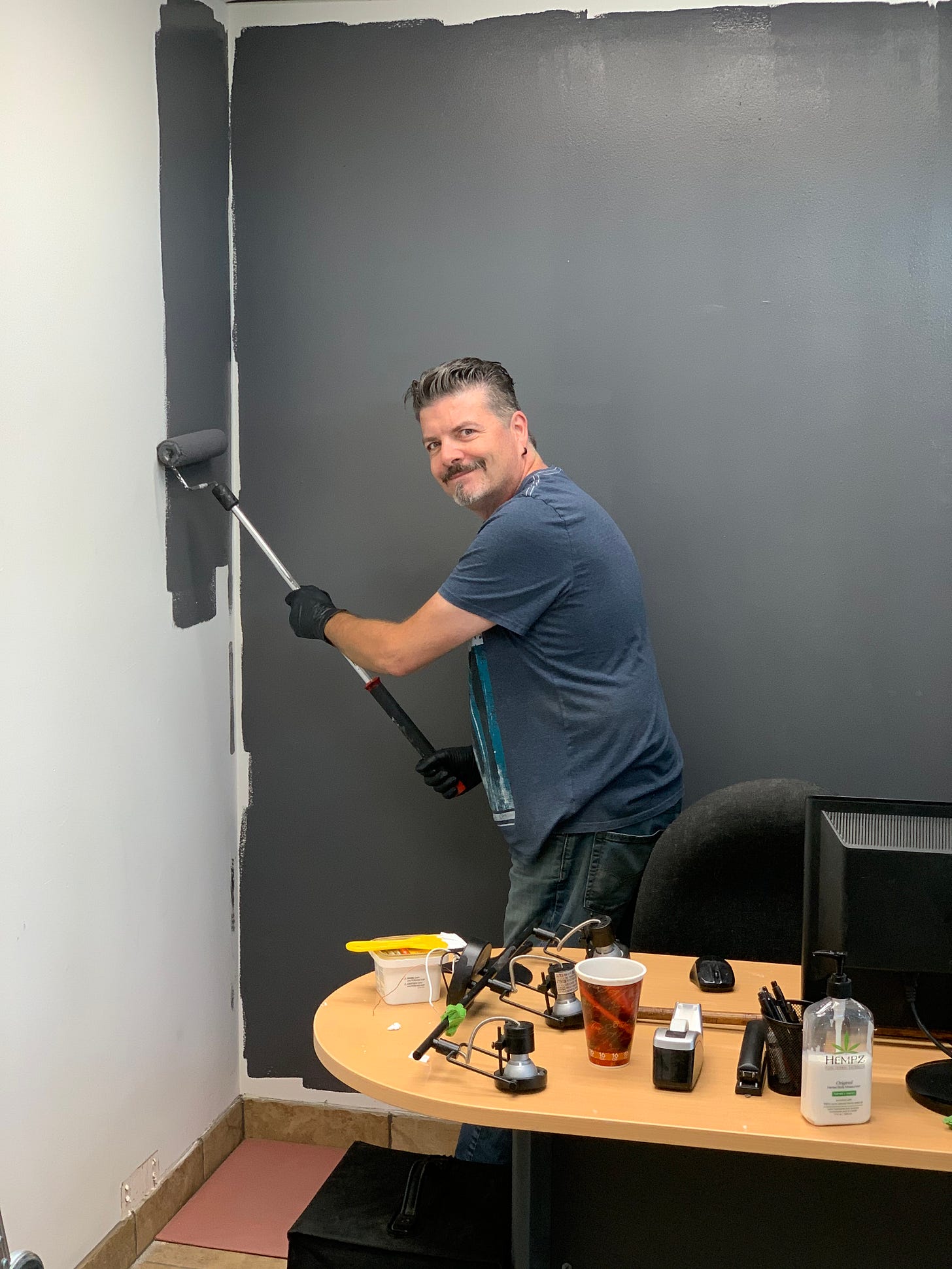
So if all that stuff was not challenging enough, perseverance and tenacity (however nonsensical in the era of the dystopian absurdities) prevailed. The ridiculous research and development (in isolation during the pandemic) added to supply delays that pretty much made people wanna crucify me! (Nothing like The feeling of being a “once upon a time” well regarded successful niche maker (of some value) to being some sort of unfair “mad scientist” pariah in unfair times beyond control! Things had to go “off script” (and sequence) just to keep the doors open during the most treacherous dispensation of time in events! (Nope, they’ll never really understand - you bad person). It has been THAT brutal though! Normal operating levels have not been seen since before 2020. Revenue neutral jobs be damned (if the shop were to survive another month without shuttering!) Therein lies the rub!
So here are the victories! Throughout the initial struggle of getting carbon fiber models built, Other (hemp) directions revealed itself over that time. Carbon fiber turned out to be a horrible choice (sounds okay but a Marathon NIGHTMARE to finish!) There was a transition where I was applying a outer flax layer and that helped a lot! Even enhanced the sound! Eventually I went to (Industrial) Hemp and developed processes that I use today! My friends, that did NOT happen overnight! Or by accident! Just dogged stubborn brut persistence whilst ducking daggers! Those bespeckled nerds in lab coats we’re of Limited help! It happened through massive R&D by fire!! In the process, The 10x evolved into the most satisfying instruments I have ever built! But not without taking some scars…and daggers! This project I thought would take two years Took nine!! (Sorry folks, did not see the hazards and detours….).
The GOAL of the 10 X was to be made out of the fewest possible parts. The caveat being that these few parts are of the best possible quality! It was a process that started in 2016 with the ViolGlide fingerboard (which went on hundreds of Instruments before it’s 10x target existed!) Basically, I started the engineering with the fingerboard (The Achilles’ heel and keystone of these instruments!) while fulfilling those orders in the Fillmore years, Evenings and odd weekends were spent making the patterns and molds. The public really has no freaking idea (zero clue actually) just how intense this 10x project really has been! (No, I really don’t sleep well). In fact I developed a second career as an industrial designer and mold engineer specializing in organic Hemp composites!!
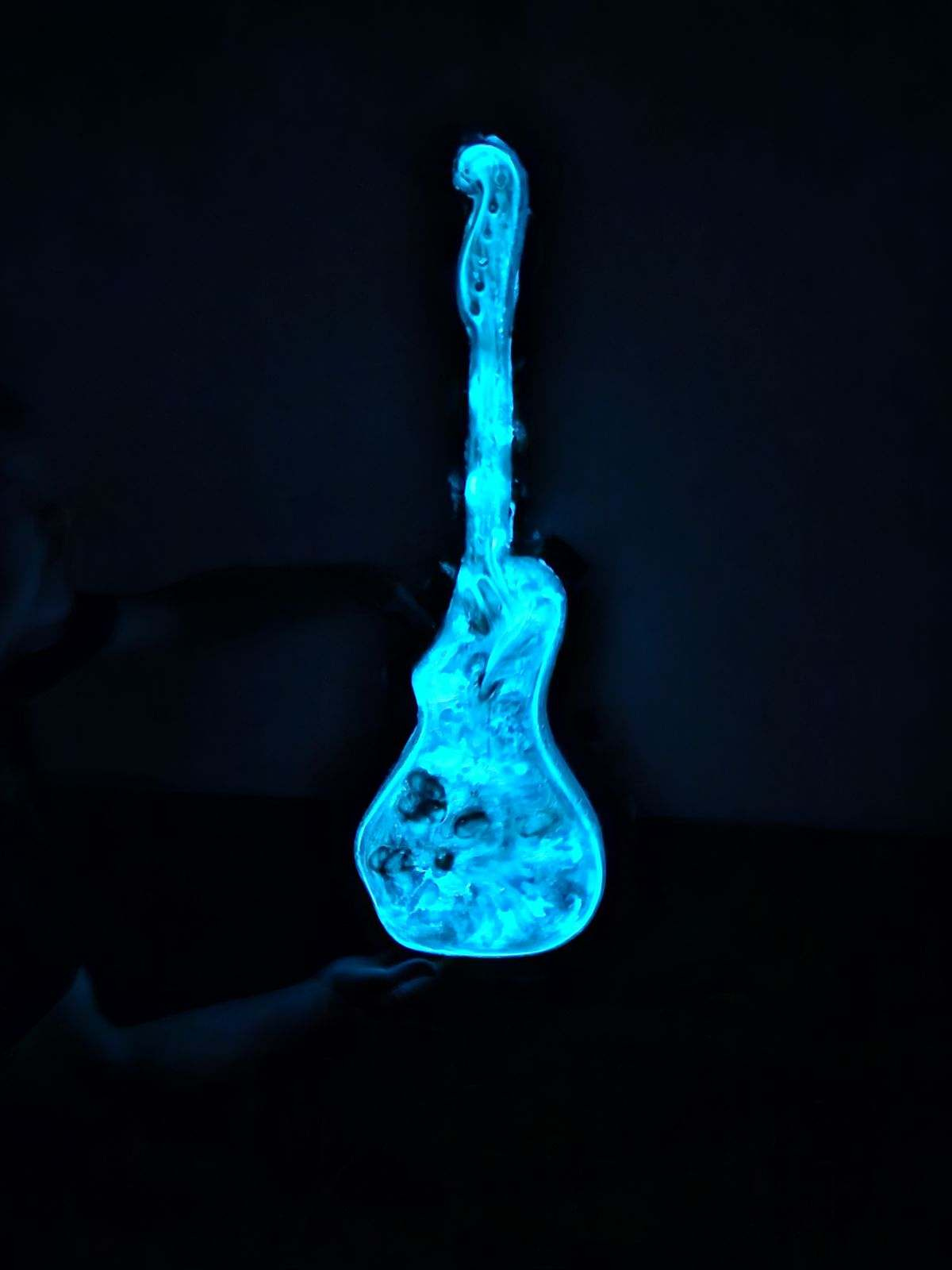
So, The ONE universal model I build is the 10x! The “Hull” (body and neck) is one seamless vacuum molded layup of hemp “Superwood”. It can be treated with different colors in various artistic touches. Even glow in the dark! Or just plain black. But don’t be fooled! It is all about superior feel and sound! The Engineered top is vacuum laminated with an outer veneer, balsa core, and hemp backing. It is strong light and very powerful! It eats traditional spruce for lunch! Better yet, it won’t crack with the coming of rain followed by desert winds. The “impossible” neck transition to the body allows unimpeded access to the second octave of the instrument; requiring “mad science” engineering! The fingerboard is the ViolGlide that has successfully been installed on all instruments since the summer of 2016. All marvels of engineering through the toughest of times! (No torture no diamonds?)
In summary, the GuitarViol has been a rough bronco ride (a misunderstood one at that!) When I started out in the late 80s early 90s (pre-Internet) virtually nobody knew (or cared) what is an Arpeggione was. Those that did thought that it was a “stupid idea” (but I knew it could be done better). Nowadays these instruments are falling out of the freaking sky on Instagram! Yes there are even copycats along with faithful traditional to Stauffer builders. Most of them doing the same mistakes I did 30 years ago. But in the last 10 years, my intention was to standardize the GuitarViol to a recognizable pattern. When you see a violin, you know it’s a Violin! You see a classical guitar, you know it’s a classical guitar! You see a GuitarViol? You know what I mean! The electric guitar world is littered with zillions of funny shapes; many of which are impractical and have no ergonomic thought put into them whatsoever (I commend those that do). So if people are confused as to why I have pushed the direction (goal) to a standardized version of an instrument that I somehow ushered into The 21st century from a failed 19th century Instrument, I hope this essay/article gives you some insight to that! It’s one thing to fight the forces of tradition, bias, nature and physics. It’s another to do it at the dawn of what seems to be some sort of dystopian globalist clown revolution where strange creatures like AI and social credit scores threaten to obscure the best of what was (if not humanity itself). For some people the GuitarViol’s response in the hand transports them to a place and time of unique beauty and creativity. Those things which bring people together.
Thank you all for joining me on this journey! One more day!
What’s next? Guitars and violins based on the 10x tech!? Sure! Just remind me to put on a parachute before I jump out of that airplane! It’s a hard landing…
Stay inspired!
Jonathan
It will be regarded in the future as a timeless instrument, a delightful marriage of ancient and modern~
Well done.